Termoplásticos
Un termoplástico es un plástico que, a temperaturas relativamente altas, se vuelve plástico, deformable o flexible, se derrite cuando se calienta y se endurece en un estado de transición vítrea cuando se enfría lo suficiente. La mayor parte de los termoplásticos son polímeros de alto peso molecular, los cuales poseen cadenas asociadas por medio de fuerzas de Van der Waals débiles (polietileno); fuertes interacciones dipolo-dipolo y enlace de hidrógeno, o incluso anillos aromáticos apilados (poliestireno). Los polímeros termoplásticos difieren de los polímeros termoestables o termofijos en que después de calentarse y moldearse pueden recalentarse y formar otros objetos.
Sus propiedades físicas cambian gradualmente si se funden y se moldean varias veces (historial térmico), generalmente disminuyendo estas propiedades al debilitar los enlaces.
Los más usados son: el polietileno (PE), el polipropileno (PP), el polibutileno (PB), el poliestireno (PS), el polimetilmetacrilato (PMMA), el policloruro de vinilo (PVC), el politereftalato de etileno(PET), el teflón (o politetrafluoretileno, PTFE) y el nylon (un tipo de poliamida).
Los más usados son: el polietileno (PE), el polipropileno (PP), el polibutileno (PB), el poliestireno (PS), el polimetilmetacrilato (PMMA), el policloruro de vinilo (PVC), el politereftalato de etileno(PET), el teflón (o politetrafluoretileno, PTFE) y el nylon (un tipo de poliamida).
Métodos de conformado
Existen varias técnicas para dar forma a los plásticos. Algunas de las más comunes son:
- Extrusión
- Inyección
- Compresión
- Soplado
- Moldeado al vacío
- Calandrado (Laminado/Hilado)
Métodos de extrusión (termoplásticos)
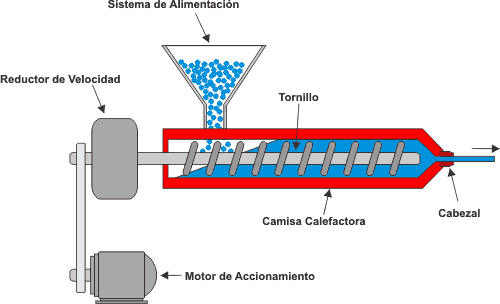
Este sistema funciona de la siguiente manera: los gránulos de plástico entra en el sistema de alimentación, estos pasan al tornillo sin fin, mientras estos gránulos se van derritiendo a causa del las camisas calefactoras, estos gránulos se van desplazando, por el movimiento giratorio del tornillo, hacia el cabezal, donde el material pasa a unos molde que le dan forma. Mas tarde se refrigeran y obtiene su forma definitiva, resistente y rígida.
Este método solo se puede utilizar en aquellos casos donde los extremos de los objetos estén cerrados o abiertos, en el caso de que solo sea un extremo el que esté abierto o cerrado, este método no funcionaria. Por ejemplo: tuberías, mangueras, marcos de ventanas, etc..
Método de inyección (termoestables)
El método de inyección es muy similar al de extrusión, los gránulos del plástico entran en el embudo, estos entran en el tornillo sin fin, y son transportados a un molde de metal, aquí se enfría y obtiene su forma final.
Este método es utilizado para formas más complicadas y de medidas diferentes,como por ejemplo: vasos, platos, carcasas de móviles, etc..

- Inyección
- Compresión
- Soplado
- Moldeado al vacío
- Calandrado (Laminado/Hilado)
Métodos de extrusión (termoplásticos)
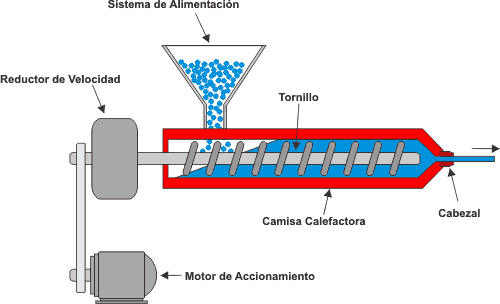
Este sistema funciona de la siguiente manera: los gránulos de plástico entra en el sistema de alimentación, estos pasan al tornillo sin fin, mientras estos gránulos se van derritiendo a causa del las camisas calefactoras, estos gránulos se van desplazando, por el movimiento giratorio del tornillo, hacia el cabezal, donde el material pasa a unos molde que le dan forma. Mas tarde se refrigeran y obtiene su forma definitiva, resistente y rígida.
Este método solo se puede utilizar en aquellos casos donde los extremos de los objetos estén cerrados o abiertos, en el caso de que solo sea un extremo el que esté abierto o cerrado, este método no funcionaria. Por ejemplo: tuberías, mangueras, marcos de ventanas, etc..
Método de inyección (termoestables)
El método de inyección es muy similar al de extrusión, los gránulos del plástico entran en el embudo, estos entran en el tornillo sin fin, y son transportados a un molde de metal, aquí se enfría y obtiene su forma final.
Este método es utilizado para formas más complicadas y de medidas diferentes,como por ejemplo: vasos, platos, carcasas de móviles, etc..

Método compresión (termoestables)
Éste método es utilizado para piezas de gran tamaño y no muy complicadas, como guardabarros de coche, pomos de puertas, pulseras,... El plástico que se trata adquiere una forma gracias a la presión de una máquina que tiene un molde. El proceso es el siguiente: se coloca una pieza de plástico en un molde de metal, esta es aplastada y moldeada por otra pieza de metal que conforma la otra mitad del molde, todo ello se realiza con el plástico a una elevada temperatura, gracias a esto el material adquiere una forma rígida, uniforme y homogéneo.

Método de soplado (termoestables)
Este método se utiliza para la creación de envases u objetos huecos, como las botellas.
Se basa en utilizar una preforma de plástico, que ha sido obtenido anteriormente por el método de extrusión, que se introduce en un molde metálico y que se adaptara a dicho molde por la introducción de aire caliente. Más tarde se enfría y se retira del molde para su uso.

Método de modelado al vacío
Este método se utiliza para la creación de vasos, platos, mascaras y todo aquello que tenga unas paredes muy finas.
Para este método se utiliza una lamina fina de plástico, la cual es calentada con unas resistencias. Debajo de esta lamina de plástico se encuentra un objeto del cual se quiere adoptar su forma, luego la lamina de plástico caliente cae sobre el molde, luego se extrae el aire para que el plástico obtenga todos sus detalles.

Método de calandrado
Este método se utiliza para la creación de placas PVC, carpetas, manteles, láminas de invernadero, etc.
Para la obtención de éstos objetos mediante este método, se introducen los gránulos de plástico procedentes de una tolva en el interior de una calandra, que es un conjunto de rodillos,donde, según el grosor que haya entre éstos, se obtendrá láminas de plástico de distinto grosor listas para su uso.

Éste método es utilizado para piezas de gran tamaño y no muy complicadas, como guardabarros de coche, pomos de puertas, pulseras,... El plástico que se trata adquiere una forma gracias a la presión de una máquina que tiene un molde. El proceso es el siguiente: se coloca una pieza de plástico en un molde de metal, esta es aplastada y moldeada por otra pieza de metal que conforma la otra mitad del molde, todo ello se realiza con el plástico a una elevada temperatura, gracias a esto el material adquiere una forma rígida, uniforme y homogéneo.


Método de soplado (termoestables)
Este método se utiliza para la creación de envases u objetos huecos, como las botellas.
Se basa en utilizar una preforma de plástico, que ha sido obtenido anteriormente por el método de extrusión, que se introduce en un molde metálico y que se adaptara a dicho molde por la introducción de aire caliente. Más tarde se enfría y se retira del molde para su uso.

Método de modelado al vacío
Este método se utiliza para la creación de vasos, platos, mascaras y todo aquello que tenga unas paredes muy finas.
Para este método se utiliza una lamina fina de plástico, la cual es calentada con unas resistencias. Debajo de esta lamina de plástico se encuentra un objeto del cual se quiere adoptar su forma, luego la lamina de plástico caliente cae sobre el molde, luego se extrae el aire para que el plástico obtenga todos sus detalles.

Método de calandrado
Este método se utiliza para la creación de placas PVC, carpetas, manteles, láminas de invernadero, etc.
Para la obtención de éstos objetos mediante este método, se introducen los gránulos de plástico procedentes de una tolva en el interior de una calandra, que es un conjunto de rodillos,donde, según el grosor que haya entre éstos, se obtendrá láminas de plástico de distinto grosor listas para su uso.

En cuanto a la reparación de termoplásticos , los métodos que hemos utilizado en el aula son básicamente dos :
Como explicación para este sistema no hay mejor modo que las instrucciones de una de estas maquinas que sueldan plásticos mediante pequeñas grapas metálicas con varias formas a convenir según el lugar que vayamos a reparar :
Reparación mediante soldadura
Aquí dejo un vídeo explicativo de una reparación de sintéticos mediante soldadura con todos los pasos perfectamente expuestos. Es un poco largo pero muy completo :
Termoestables
La estructura altamente reticulada o unida mediante enlaces químicos que poseen los materiales termoestables, es la responsable directa de las altas resistencias mecánicas y físicas (esfuerzos o cargas, temperatura...) que presentan dichos materiales comparados con los materiales termoplásticos o elastómeros.
Por contra es dicha estructura altamente reticulada la que aporta una pobre elasticidad a dichos materiales, proporcionando a dichos materiales su característica fragilidad.
Imaginemos que encima de una mesa tenemos un conjunto de cuerdas entremezcladas unas con otras, cada uno de estas cuerdas es lo que llamamos polímero, tendremos que aplicar poco esfuerzo si queremos separar las cuerdas unas de otras, ahora comenzamos a realizar nudos entre cada una de las cuerdas, apreciamos que conforme más nudos realizamos más ordenado y rígido se vuelve el conjunto de las cuerdas, cuanto más nudos realicemos más esfuerzo necesitaremos aplicar para separarlos, en este simil los nudos representan los enlaces químicos, que hacen a los polímeros estar fuertemente unidos unos con otros y formar estructuras poliméricas altamente reticuladas, o lo que es lo mismo formar materiales termoestables.
Unos los parámetros característicos de los materiales termoestables es el punto de gelificación o punto de gel, el cual se refiere al momento en el que el material pasa de una manera irreversible de un estado liquido-viscoso a un estado sólido durante el proceso de curado o reticulado, una vez se ha traspasado dicho punto de gelificación el material deja de fluir y no puede ser moldeado o procesado de nuevo.
Uno de los aspectos negativos de los materiales termoestables es la nula capacidad de reciclaje que presentan dichos materiales, dado a que una vez han solificado o curado es imposible volver a una fase líquida del material, los materiales termoestables tienen la propiedad de no fundirse o deformarse en presencia de temperatura o calor, antes pasarán a un estado gaseoso que a un estado líquido.

No se pueden derretir, antes de derretirse pasan a un estado gaseoso
Generalmente no se hinchan ante la presencia de ciertos solventes
Son insolubles.
Alta resistencia al fenómeno de fluencia
Ejemplos y aplicaciones de materiales termoestables:
Generalmente no se hinchan ante la presencia de ciertos solventes
Son insolubles.
Alta resistencia al fenómeno de fluencia

Resinas epoxi - usados como materiales de pintura y recubrimientos, masillas, fabricación de materiales aislantes, etc...
Resinas fenólicas - empuñaduras de herramientas, bolas de billar, ruedas dentadas, materiales aislantes, etc...
Resinas de poliéster insaturado - fabricación de plásticos reforzados de fibra de vidrio conocidos comúnmente como poliester, masillas, etc...
Ejemplos de adhesivos termoestables:
Resinas fenólicas - empuñaduras de herramientas, bolas de billar, ruedas dentadas, materiales aislantes, etc...
Resinas de poliéster insaturado - fabricación de plásticos reforzados de fibra de vidrio conocidos comúnmente como poliester, masillas, etc...

Adhesivos de Epoxy
Adhesivos de Poliéster insaturados
Adhesivos de Poliuretano de 1 componente curado mediante calor
Adhesivos anaeróbicos
Fabricación de moldes y piezas de elementos termoestables.
Estamos hablando en términos generales aunque depende también la configuración de la pieza. Una vez fabricado el molde como en el proceso de transformación se emiten gases se les suele dar unos baños químicos que facilita el desmoldeado de la pieza.
Para su protección y desgaste se acostumbran a darlos un tratamiento de cromo titanio y niquel que también ayuda a mejorar el aspecto superficial de la pieza. La vida aproximada de un molde con estos materiales a transformar es de 1MM de inyectadas aunque disminuye si los materiales llevan cargas.
Los moldes de poliésteres son de otro acero que llevan más contenido en cromo que facilitan el desmoldeo, con un tratamiento superficial a 58-60 HRC.
El termoestable es un material más abrasivo que cualquier plástico, por tanto los moldes acostumbran a ser más caros ya que al emplear materiales de más dureza el tiempo de mecanizado es superior. También debemos significar que al ser materiales tan abrasivos es importante tratar a la zona de inyección de forma empostizada ya que es la parte del molde más sometida a desgaste y con mayor influencia a una posible variación de medidas.
Los moldes de termoestables están provistos generalmente de resistencias internas tubulares que lo calientan entre 140-180ºC según el tipo de material. A veces también van provistos de resistencias planas externas con lo que obliga a colocar placas aislantes en las caras del molde para evitar la fuga de calor, definiendo el espesor de la pieza la medida que marca el grosor de dicha placa.
Estos materiales permiten igual que en los plásticos realizar cualquier roscado en el proceso de transformación . La diferencia es que los mecanismos son más complejos y tiene una duración más limitada que en los plásticos porque están sometidos a un desgaste mayor debido a las altas temperaturas.
El sistema de colada para la inyección de estos materiales es similar al de los termoplásticos, o sea inyección submarina y directa. Utilizar un tipo u otro lo determina la configuración de la pieza.
Adhesivos de Poliéster insaturados
Adhesivos de Poliuretano de 1 componente curado mediante calor
Adhesivos anaeróbicos
Fabricación de moldes y piezas de elementos termoestables.
Una de las cosas a destacar en los moldes a fabricar piezas de resinas fenólicas o aminoplastos es que están sometidos a altas temperaturas y desgates como hemos visto anteriormente, por tanto utilizamos un acero 2379 ya que es un material de una dureza considerable y después sometido a un tratamiento térmico de 58-60 HRC.
Estamos hablando en términos generales aunque depende también la configuración de la pieza. Una vez fabricado el molde como en el proceso de transformación se emiten gases se les suele dar unos baños químicos que facilita el desmoldeado de la pieza.
Para su protección y desgaste se acostumbran a darlos un tratamiento de cromo titanio y niquel que también ayuda a mejorar el aspecto superficial de la pieza. La vida aproximada de un molde con estos materiales a transformar es de 1MM de inyectadas aunque disminuye si los materiales llevan cargas.
Los moldes de poliésteres son de otro acero que llevan más contenido en cromo que facilitan el desmoldeo, con un tratamiento superficial a 58-60 HRC.
El termoestable es un material más abrasivo que cualquier plástico, por tanto los moldes acostumbran a ser más caros ya que al emplear materiales de más dureza el tiempo de mecanizado es superior. También debemos significar que al ser materiales tan abrasivos es importante tratar a la zona de inyección de forma empostizada ya que es la parte del molde más sometida a desgaste y con mayor influencia a una posible variación de medidas.
Los moldes de termoestables están provistos generalmente de resistencias internas tubulares que lo calientan entre 140-180ºC según el tipo de material. A veces también van provistos de resistencias planas externas con lo que obliga a colocar placas aislantes en las caras del molde para evitar la fuga de calor, definiendo el espesor de la pieza la medida que marca el grosor de dicha placa.
Estos materiales permiten igual que en los plásticos realizar cualquier roscado en el proceso de transformación . La diferencia es que los mecanismos son más complejos y tiene una duración más limitada que en los plásticos porque están sometidos a un desgaste mayor debido a las altas temperaturas.
El sistema de colada para la inyección de estos materiales es similar al de los termoplásticos, o sea inyección submarina y directa. Utilizar un tipo u otro lo determina la configuración de la pieza.
Reparación de termoestables:
Aquí dejo el enlace de un vídeo de una reparación de elementos termoestables mediante el uso de adhesivos :
Espero que esta entrada sirva de ayuda a todo aquel que lo necesite. Un saludo
Hola estoy por comenzar a estudiar este curso de chapista pintor de vehículos, y me gustaría si alguien la conoce ya que estoy un poco nervioso, por favor decirme como son?
ResponderEliminar